Ask the expert: Single-use systems
Ken Wong, Sanofi’s Head of Procurement for Asia, tells us about the benefits and challenges of using single-use systems in pharma manufacturing and the supply chain
Add bookmark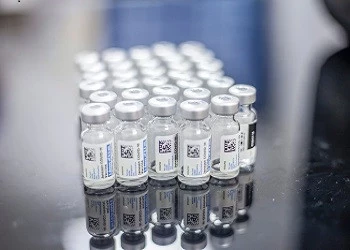
Pharma Logistics IQ: Why are drug manufacturers shifting to disposable equipment and single-use systems?
Ken Wong: Fixed equipment involves a lot of capital and time for validation. In drug development speed is everything. If you have competitors developing the same drug, the company with the best speed-to-market will corner the market share. Single-use systems enable this speed.
You may not adopt them internally but you might select a contract manufacturing organization (CMO) that uses single-use systems to produce quickly without the need to build your equipment. Covid-19 demonstrated this, because the speed needed to develop drugs was so fast that there was no way to match that manufacturing time without single-use equipment.
Looking ahead, using AI-assisted technology will make the manufacturing process even faster and single-use systems will be pivotal to this.
Read our full report on single-use systems: how to overcome challenges and mitigate risk in bioprocessing
Pharma Logistics IQ: How does single-use equipment fare on sustainability?
KW: We cannot recycle these items because it is biomedical waste, and discarding it is not an easy process until we find a different way to solve it. However, modelling was done a couple of years ago that found that the water and energy savings made from not having to sterilize single-use equipment can offset the issue of waste.
Pharma Logistics IQ: What challenges does shifting to single-use equipment present pharma manufacturers?
KW: For small molecule companies that produce a high volume of generic drugs, the operational cost for single-use equipment is higher than it is for fixed stainless steel equipment because the daily expense for consumables is higher. For that reason, generics companies are typically less likely to adopt single-use, however we are seeing hybrid systems more and more at these companies producing smaller volumes.
We are also seeing a higher demand for single-use equipment right now and suppliers cannot keep up with this demand. For the last two years sub-suppliers are also struggling to keep up with demand, so there has been a knock-on effect on parts all the way up to assembly lines. For example, there is a shortage of plastic and cardboard packaging that, even though it is not obvious to most people, is hindering the supply chain.
There is also a driver shortage, so the delivery of shipments is slow and sometimes not dependable, and there are delays clearing customs for shipments that are crossing countries. This is leading to a new approach where pharma companies produce for their region only.
Read how to shift to single-use assemblies to protect complex drug products
Pharma Logistics IQ: What can be done to address these supply shortages?
KW: All the different related shortages – packaging and raw materials, sterilization equipment, manpower and people in shipping – must be resolved. The cost of materials has also been increasing in the last few years becoming a barrier for companies starting out. Companies buying small quantities cannot negotiate the price down because they do not have the purchasing power of a larger organization. My hope is that we will see a lot of suppliers expanding in different production lines and regions sometime next year.
I am also seeing more flexibility because of the supply shortages. Most people in quality and regulatory areas are used to the old concept of Quality-by-Design (QbD), where different quality attributes are similar. Single-use systems offer a new degree of freedom, and there is a global push right now to establish some guidance for them to become more broadly adopted in the future.
Get exclusive access to member-only articles, reports, videos, interviews, webinars and other premium content from industry experts and thought leaders by signing up to Pharma Logistics IQ here.